A Success Story of how TagPoint helps eliminate paper, enhance accuracy, and streamline processes, maximising warehouse inspection efficiency.

Case
Facility
Warehouse
Implementation goals
Minimise human errors in the inspection process and enhance preventive problem detection.
Transition to a digital system and reduce reliance on paper documentation.
Ensure compliance with regulations and industry standards.
Increase work efficiency by saving time spent searching for information in paper logs.
Results
Successful implementation of TagPoint within 3 weeks. Efficient training of a 30-person staff in just one day. Configuration of three types of inspections: forklifts, racking, and lorries. Complete elimination of paper logbooks and checklists, leading to enhanced accuracy and streamlined processes.
In this article we'll uncover the challenges of manual accounting, the potential risks involved, and how TagPoint transformed the way inspections are conducted. Discover how 3-step automation simplifies processes, reduces paper usage, and boosts overall efficiency in the workplace.
Step 1. Forklifts inspections
Problems before implementation
It is our customer's practice to inspect forklifts comprehensively at their warehouse. There are two primary types of inspections:
Previously, all inspection and maintenance data were recorded in logbooks or inspection checklists, which were printed or handwritten.
Disadvantage of printed logbooks
Why is this approach problematic?
- There is a high risk of manual errors.
Paper-based approach risks human errors, leading to confusion and inaccurate records. Plus, it can be time-consuming, particularly when there are multiple forklifts to inspect.
- Data accessibility is often hindered.
Such logbooks can easily get lost or damaged, which makes it difficult to access important information like maintenance history or recurring issues. As a result, it becomes difficult to collect data from various inspections or create detailed reports.
- And there is an environmental impact.
Dependence on traditional pen-and-paper methods means you'll need a steady supply of paper, printing resources, and physical storage space. This can become costly and environmentally unsustainable.
Why going digital helps
How TagPoint Addresses These Issues
To get everything set up, the warehouse manager first placed TagPoint QR labels to all the forklifts, making sure that future inspections could be easily tracked and accounted for.
The main rule here is simple: it is necessary to place QR code labels in a noticeable place and tell employees what the labels are for.
Example of placing the QR code on the forklift
If you're interested in learning more, read how QR codes enhance maintenance and operational processes.
Next, the TagPoint team set up checklists that are relevant to the warehouse in the system.
In simple words: we transferred all inspection requirements and control questions from paper logs to digital.
During inspections, employees can simply scan the QR code to access equipment details and the relevant checklist instantly.
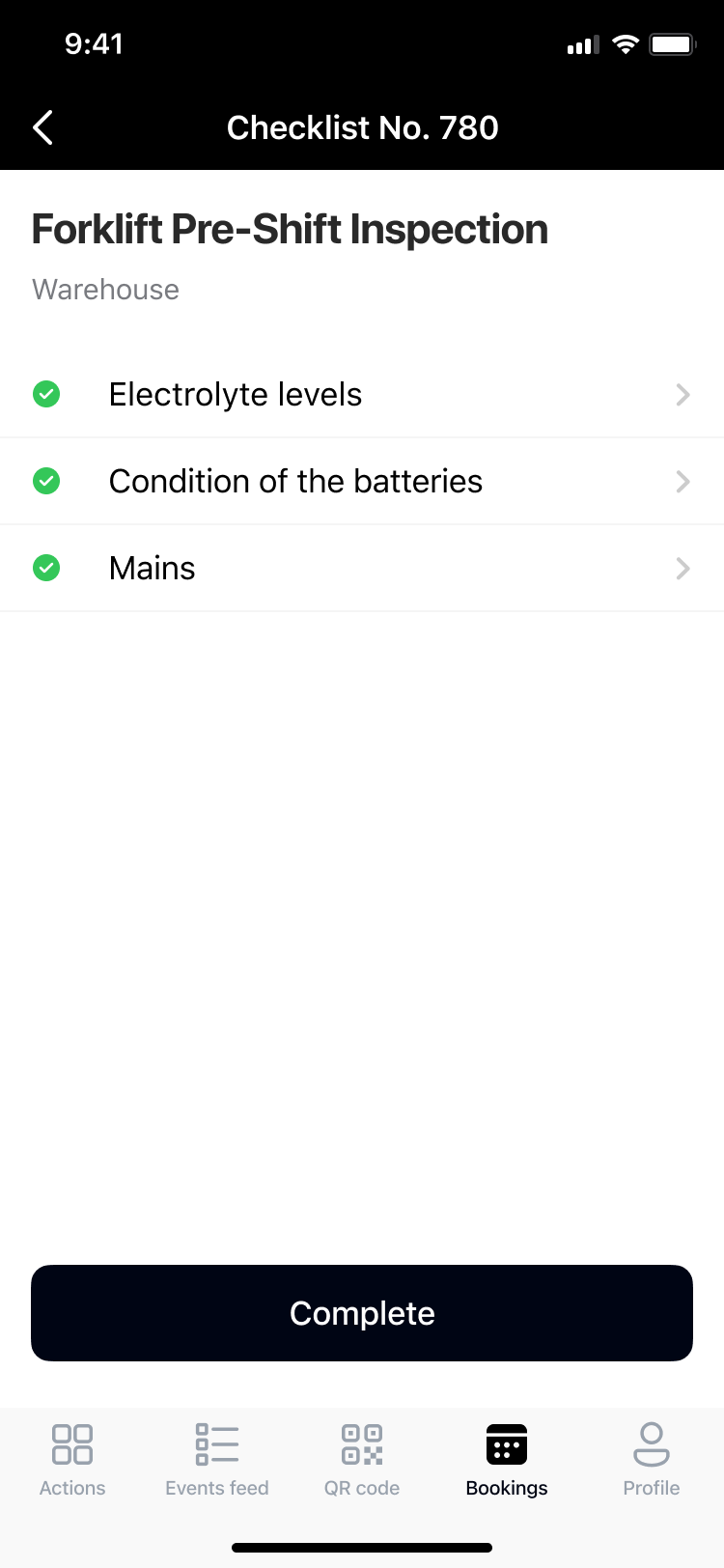
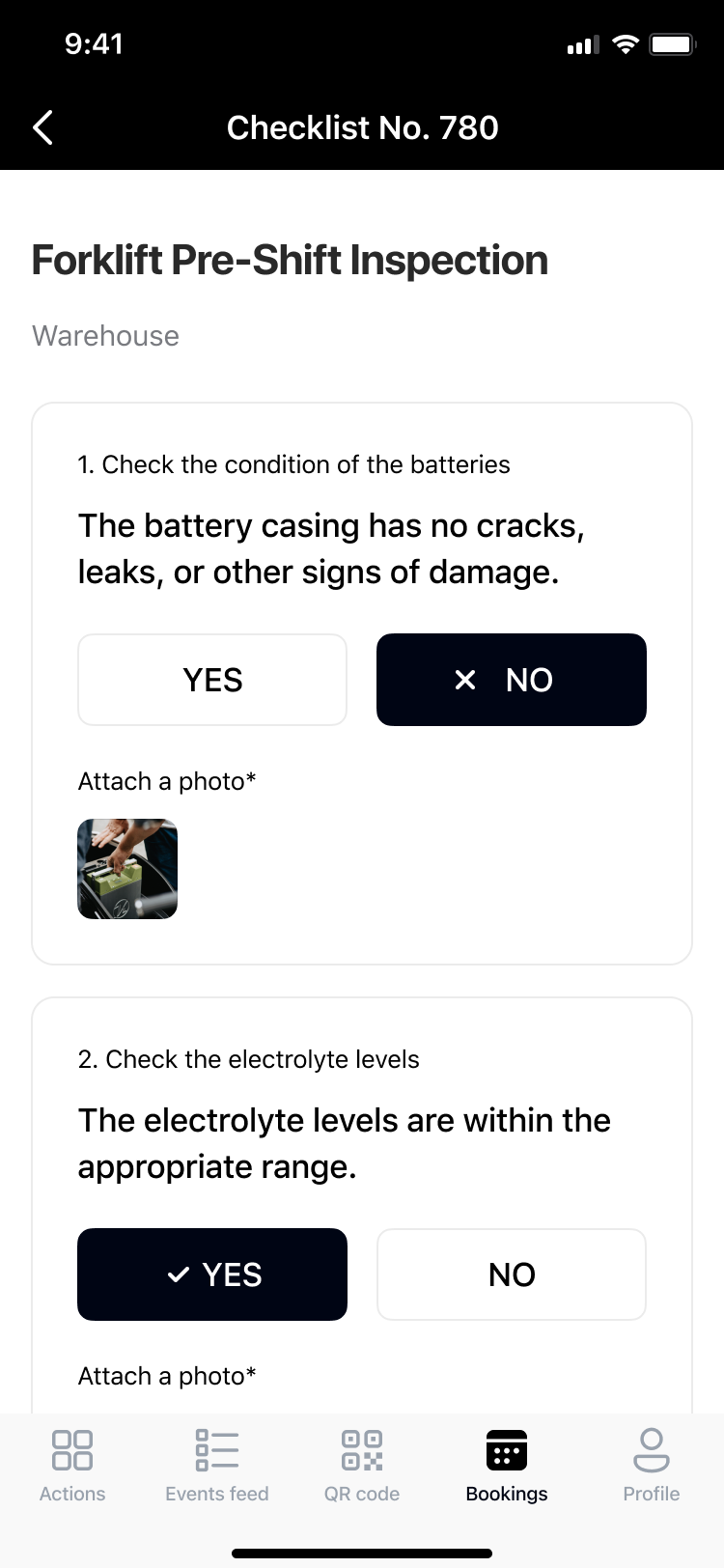
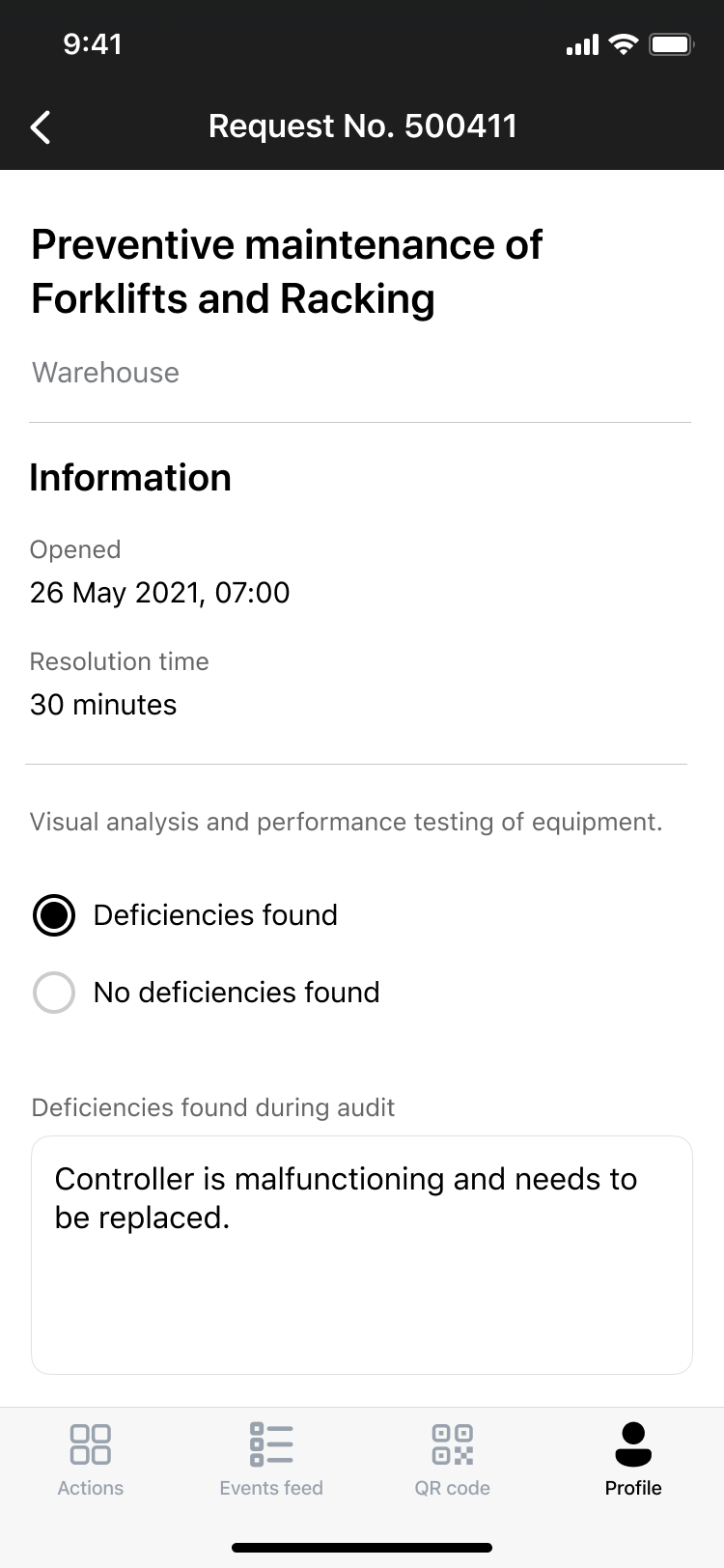
TagPoint's inspection checklists
There is also an automatic scheduling feature to streamline the process.
Automatic requests are generated based on regulatory inspection timeframes, eliminating the need for manual requests. This approach works effectively for preventive maintenance.
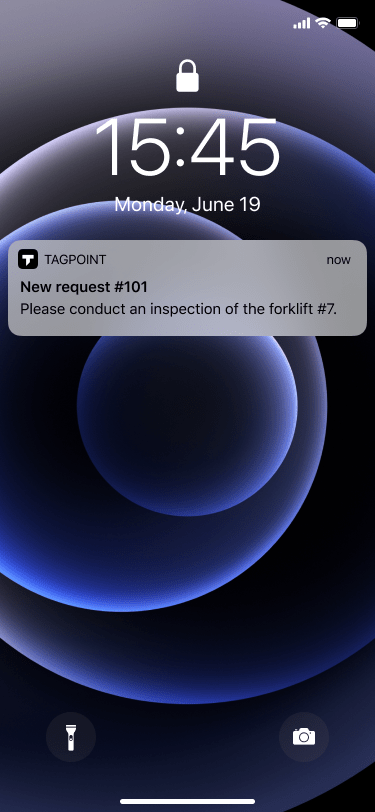
Push-notification for inspection
And finally, all inspection data is included in automatic reports. A couple of clicks provide instant access to the necessary information.
Analytical dashboards in the TagPoint system
Now, our client has a streamlined process where all forklift inspections are conducted on schedule, and the data is stored securely in the TagPoint log, accessible at any time. Automatic reports save time and effort in decision-making processes.
With digital solutions you only need a phone to conduct an inspection
Step 2. Racking inspections
Prior to TagPoint implementation, the racking inspection process resembled that of the forklifts. It involved printed checklists and logbooks, with an assigned employee conducting inspections on a rotational basis over a span of one to two weeks.
However, relying on printed or handwritten documentation for racking inspections presents similar challenges as seen with forklift inspections. It is prone to errors, has limited accessibility, and is time-consuming to manage and update.By digitising this process, we were able to overcome these issues.
First, we placed QR codes on each racking, enabling easy identification and access to information.
Example of placing the QR code on the racking
Next, there were pertinent checklists and automated reports. So when employees conduct the racking inspections, they fill out the appropriate checklists and attach necessary photos.
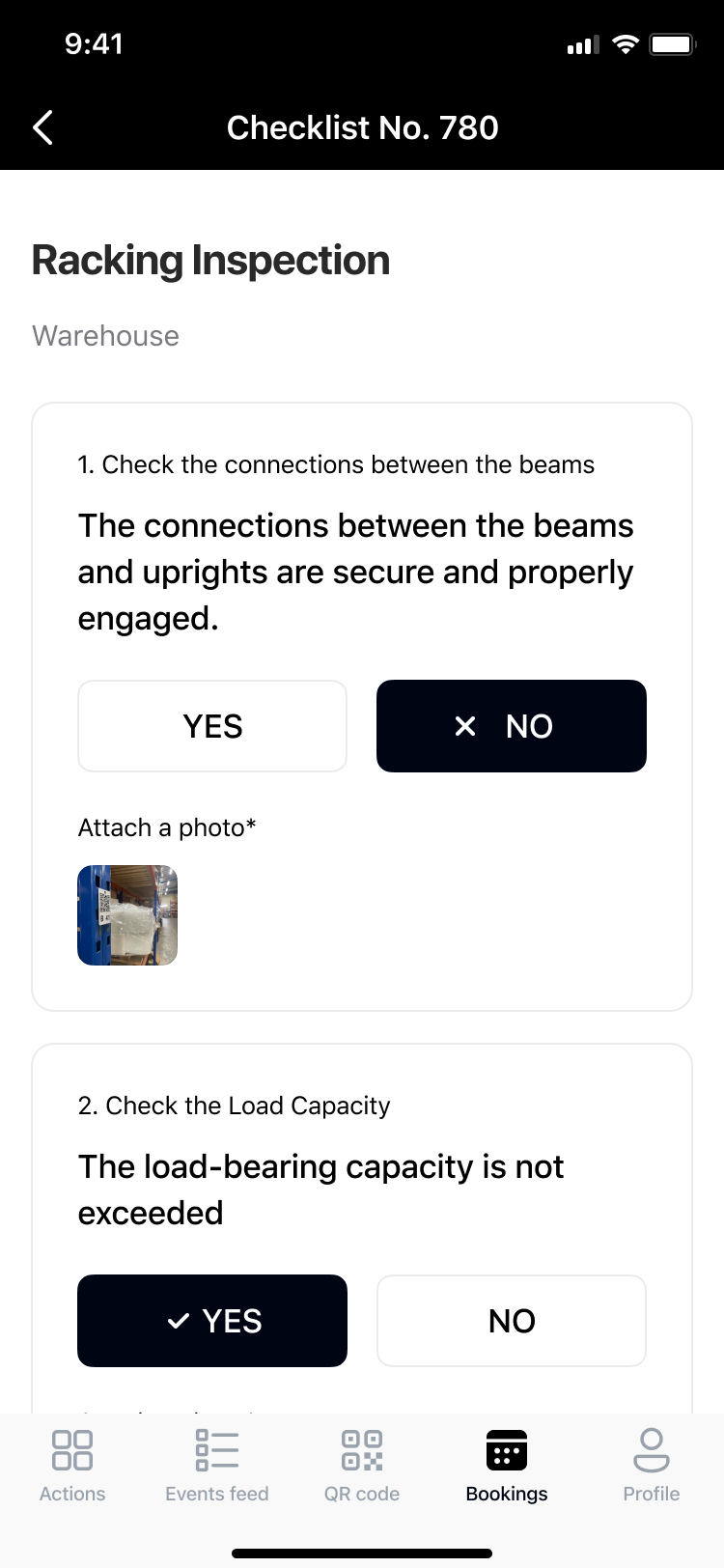
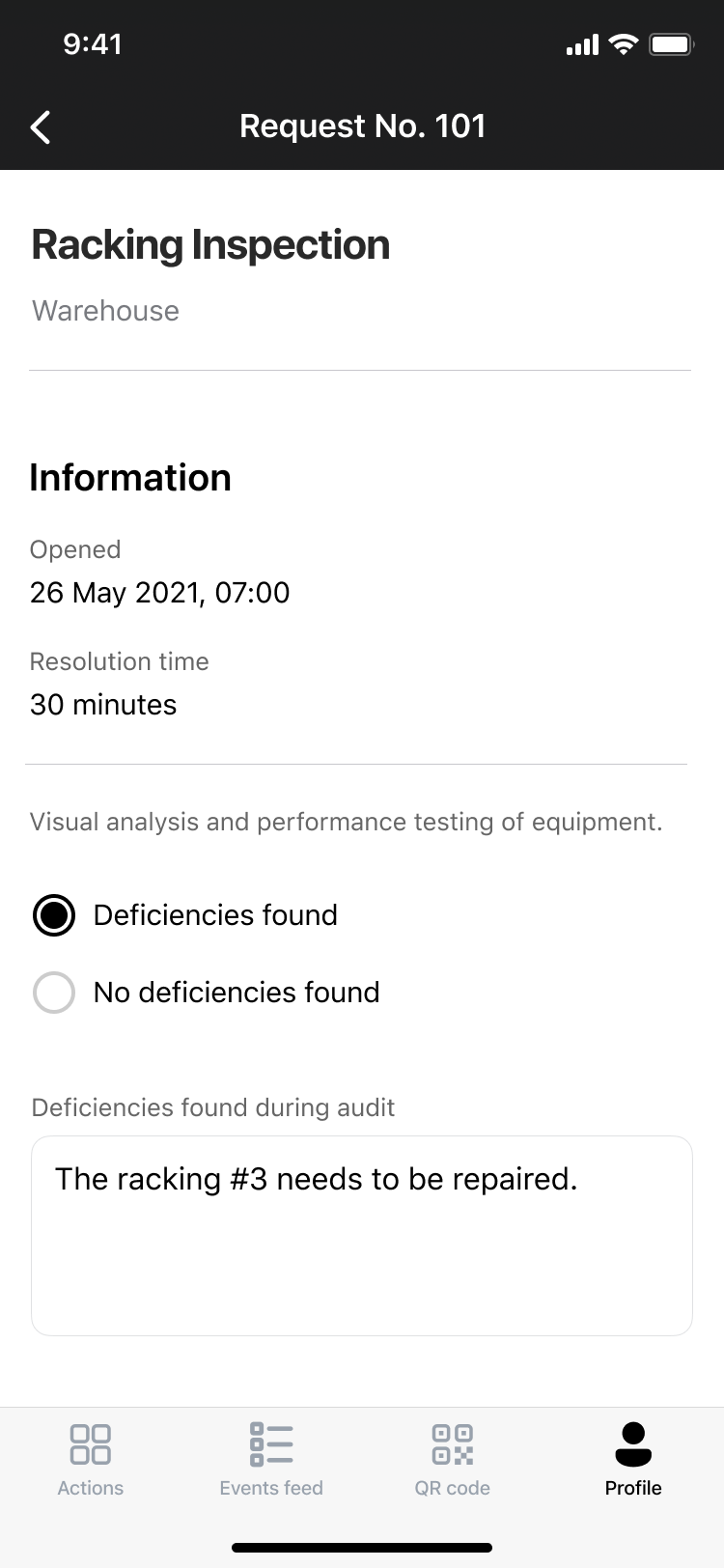
Racking inspection checklist and details
If any issues are identified, they are automatically transformed into tasks and assigned to the employees responsible for resolving them. It ensures that racking inspections are conducted consistently.
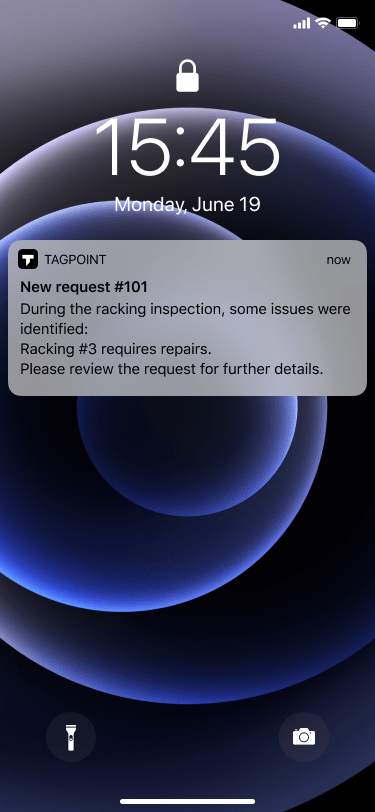
New request push notification
Lorry inspections
In response to our clients' needs, we have recently implemented this type of inspection. Here are the key reasons why they consider it absolutely essential and beneficial:
- Safety
Regular lorry inspections help keep them in line with safety rules. By checking important parts like brakes, tires, and steering, potential safety risks can be found and fixed early on. This reduces the chances of accidents or breakdowns that could harm drivers and the public.
- Compliance
It is crucial to comply with lorry inspection regulations to avoid penalties and legal troubles.
- Operational efficiency
Smooth operations depend on the maintenance of well-functioning lorries. By preventing breakdowns and delays, lorries can remain in optimal condition for transportation tasks, ensuring seamless operations.
The lorry inspection process again is streamlined with the use of QR codes, making the entire procedure more efficient.
Example of placing the QR code on the lorry
When the driver scans the QR code, they gain instant access to the specific checklist for that type of inspection. They can then proceed to perform the necessary checks while referring to the checklist. All the inspection information is stored in TagPoint, ensuring easy access with just a few clicks.
Advantages of using an app for lorry inspections
Results and summary
The progress achieved so far is good:
-
Over the course of six months, the employees conducted almost 8000 inspections on 233 warehouse bays.
-
The managers have successfully eliminated paper consumption by completely transitioning from printed logbooks and checklists to digital formats.
-
As a result, the percentage of problems detected preventively has increased, leading to a reduction in unexpected breakdowns and equipment failures.
If you are still not convinced that digital inspections surpass traditional methods, take a look at this comparison table.
Comparison: how two approaches differ
TagPoint is not limited to the inspections functionality discussed in this article. We are prepared and enthusiastic about working in similar and diverse fields. Whether it's basic warehouse needs such as fire alarm and first aid kit box inspections, or complex and non-standard processes, we are ready to assist.
Please don't hesitate to reach out to us for further information.